Rotary Cookware Bottom Heating Machine
Rotary Cookware Bottom Heating Machine
The accumulation of knowledge and experience, the crystallization of wisdom and diligence, and the product of combining theory and practice.
This equipment is a product carefully developed by our company's scientific research personnel based on fully absorbing similar product technologies at home and abroad and summarizing their years of debugging and maintenance experience. It is mainly used for heating multi-layer composite bottom pressure bonding of stainless steel pots, pots, and other catering utensils.
◎ Composite bottom heating machines generally include the following three parts:

Introduction to Heating Power Supply
◎ The existing heating machine power supply in China generally adopts the following three types:
◆ Electronic tube high-frequency: It is a traditional technology with a long history. It uses high-voltage vacuum transistors as frequency conversion main devices to convert the three-phase 380V/50HZ power supply commonly used in domestic factories into high-frequency currents ranging from tens to hundreds of kilohertz through voltage regulation, boosting, rectification, self-excited oscillation of electronic tubes, and DC isolation. This technology was widely used before 2000 and is now almost phased out.
◆ Controllable silicon intermediate frequency: Controllable silicon, also known as thyristor, English symbol SCR. It uses controllable silicon to convert a 380V/50HZ power supply into an intermediate frequency current of several thousand hertz through rectification, voltage regulation, flat wave filtering, and inversion. It is a frequency conversion technology that rapidly developed in the 1970s and 1980s. It was widely used in composite bottom heating machines in China from 2000 to 2008 and partially replaced high-frequency electronic tubes.
◆ IGBT ultrasonic frequency: Similar to the above-mentioned thyristor power supply, the difference is that the inverter part uses high-power transistor IGBT (also known as "insulated gate bipolar transistor") frequency conversion, which has a higher switching speed and generates a higher frequency than the thyristor, generally reaching tens of kilohertz. It is a technology that rapidly developed in the 1990s. It is now widely used in composite bottom heating machines and has basically replaced the two power sources mentioned above.
Our company has successfully developed a rotary composite bottom heating machine, and its power supply adopts all the modulation wave frequency conversion technology successfully developed by our company's researchers in China after years of dedicated research. This technology uses high-power switching device "field-effect transistor MOSFET" as the inverter element. Absorbing all the advantages of the above three technologies and overcoming their respective shortcomings, it is an upgraded product of the heating machine and will be widely applied.
This technology uses embedded microcomputers as the core and other peripheral devices. Based on the powerful functions of computer software and hardware, it realizes the adjustment of current changes.
◎ Compared to the original three power sources, it has the following advantages:
◆ Uniform heating and high product quality: Due to the fact that the output current of our equipment is a combination of several currents with significant differences and different frequencies, the areas of induction heating and the depth of heat transmission caused by different frequencies of currents are different. Therefore, the temperature difference in different areas of the heating element is much smaller than that of the original three power sources, resulting in good quality of the bottom of the pot produced;
◆ Electricity and water saving: Due to uniform heating, it greatly reduces the power loss caused by local high temperatures; Tests have shown that this device saves about 30% to 50% of power compared to the other three power sources.
◆ Fast heating speed: Due to uniform heating, there is no need to worry about local overheating and melting, and the power can be increased as much as possible for faster production.
◎ Compared to high-frequency electronic tubes, there are several other advantages:
◆ Small size and light weight: Due to the small size of the main power devices (MOSFETs), the volume is more than 30% smaller than that of electronic tube devices of the same specification, saving space and facilitating installation;
◆ Easy to operate: it can be used immediately and stopped immediately, without the need for preheating before starting up or continuing cooling after stopping, reducing work time waste.
◆ Usage: Electronic tubes belong to high-voltage devices and have a high voltage of tens of thousands of volts during operation, while MOSFETs are low-voltage devices with a peak voltage not exceeding 500 volts, which generally does not cause personal injury.
Introduction to Heating Machine Tool
This equipment adopts a rotating structure, with 6 workpiece support heads evenly distributed on the cast aluminum turntable, and the turntable rotates at a 60 degree angle each time; Pneumatic lifting and lowering; Install four or five induction heads for simultaneous heating, with each pot bottom heated four to five times.
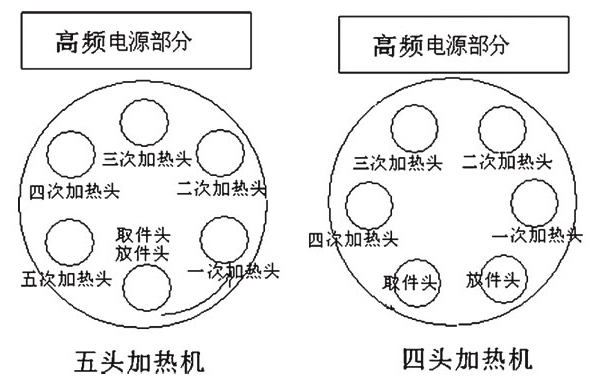
◎ Compared to inline heating machines, rotary machine tools have the following advantages:
◆ Each pot is heated multiple times by multiple induction heads, and each induction head can be adjusted to different sizes, resulting in more uniform heating. The temperature difference between the center and edge is very small, and the heating effect of all pots is basically the same, ensuring the quality of the base;
◆ The operator can stay in a fixed position and pick up and place the workpiece without moving back and forth; The equipment automatically operates in a loop, eliminating the need to lift the arm and press the power button after each pot is placed. Workers can sit on chairs to work, greatly reducing labor intensity;
◆ The picking and placing of workpieces are all carried out outside the turntable, with a large rotating space and convenient picking and placing. The height of the pot is low and unrestricted, with a wide range of applications;
◆ Facilitate future automation transformation and further save manpower.
◎ Compared with rotary machine tools from other manufacturers, there are several advantages:
◆ Multiple induction heads: Other manufacturers usually install three induction heads, while we install four or five induction heads. In this way, the power burden of each induction head is reduced, it is not easy to burn out, and the temperature at the bottom of the pot is more uniform.
◆ Using cast aluminum turntables: Other manufacturers generally use iron plates to weld and process turntables, which are heavy, easy to rust, and difficult to install and maintain; Mechanical inertia is large and easy to damage the indexing device; Internal stress is difficult to dissipate and deforms over time. And we use a cast aluminum turntable, without the aforementioned drawbacks;
◆ Large caliber cylinder: Other manufacturers generally use cylinders with a diameter of 125mm, while we use cylinders with a diameter of 160mm, resulting in high pressure and tighter contact between the heating element and the bottom of the pot, fast heat transfer, and low loss.
◆ Adopting embedded microcomputer control, with strong anti-interference ability and high reliability;
◆ Digital display of working status for easy operation and maintenance.
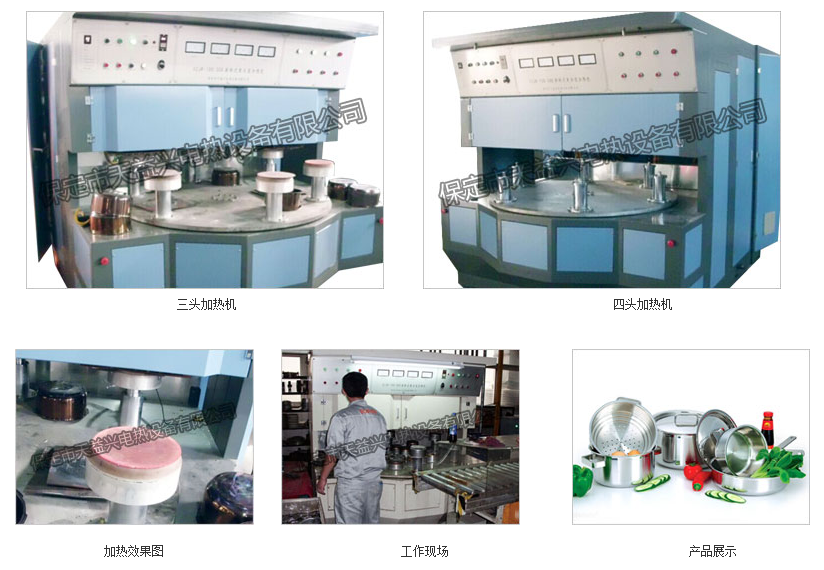